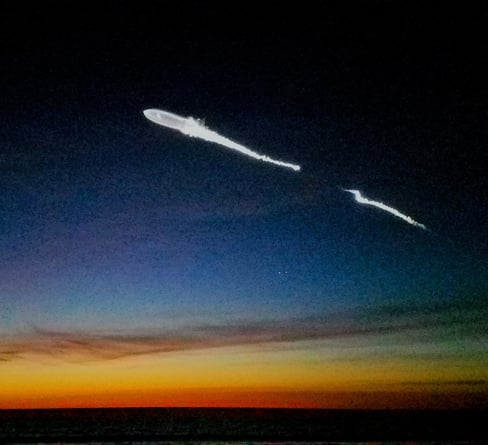
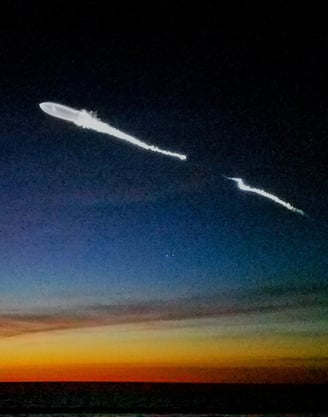
Mechanical design and analysis
Supporting teams that need:
Concept generation for new or upgraded products with structural or moving components
Rapid mechanical design using Solidworks, NX, Fusion 360 or your CAD system of choice.
Validation of new or existing designs using FEA to get it right the first time.
Clean and detailed engineering drawings to help shops make exactly what you ask for
Test plans to satisfy internal or external certification requirements
Wild Engineering LLC
― Specialties
Mechanical design
Structural analysis
Project management
Requirements development
Rapid iteration and prototyping
Mechanical test design and execution
― CAD software
Solidworks
Fusion
NX
― ANALYSIS software
ANSYS Mechanical
Femap with NASTRAN
― Past interesting projects
Let's talk
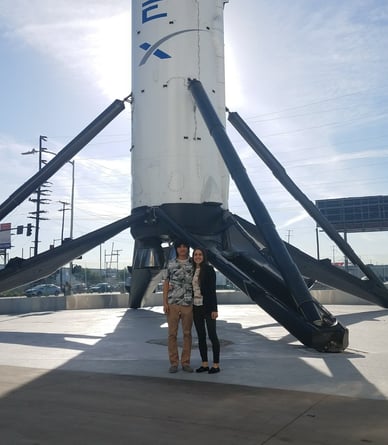
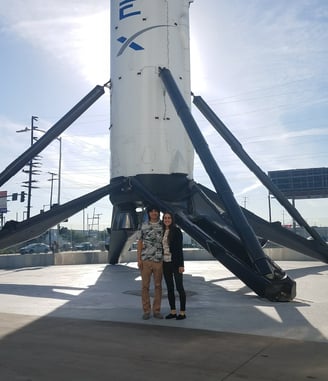